Compartimentazione antincendio
INTRODUZIONE
Per prevenire e contrastare un incendio è necessario conoscere le cause e le condizioni che ne favoriscono l’innesco e lo sviluppo. In questo paragrafo e nei successivi approfondiamo gli elementi di base dell’incendio e delle misure applicabili affinché:
- l’incendio non si verifichi;
- l’incendio non si propaghi;
- le persone coinvolte siano rapidamente poste in salvo;
- fiamme e gas possano essere estinti al più presto.
Queste conoscenze ci permetteranno di comprendere meglio la differenza tra i concetti di prevenzione, protezione passiva e attiva a cui faremo rapidamente cenno prima di focalizzare l’attenzione su protezione strutturale e compartimentazione, i due macro ambiti della protezione passiva al fuoco.
L’ultima parte dell’introduzione tratta con maggiore dettaglio la compartimentazione di aree che presentino discontinuità lungo il loro perimetro, con particolare attenzione agli attraversamenti di impianti meccanici ed elettrici, nonché ai giunti di dilatazione.
L’incendio è la combustione "non controllata" di solidi, liquidi o gas in un luogo non preparato allo scopo, o in un momento imprevisto, a seguito di un’accensione di tipo termica, meccanica, elettrica o umana. In termini più tecnici si tratta di una reazione di ossidoriduzione esotermica in cui un “combustibile” (1) si ossida e un “comburente” (2) si riduce, tramite una fonte di innesco (3).
(1) I combustibili sono le sostanze in grado di reagire con l’ossigeno (o con un altro comburente). Possono essere classificati in base allo stato fisico differenziandosi in combustibili solidi, liquidi e gassosi, in grado di produrre energia termica a seguito di una reazione di combustione. Caratteristica fondamentale di ogni combustibile è il proprio potere calorifico ossia la quantità massima di energia che può essere ottenuta dalla combustione completa di una quantità unitaria di combustibile in condizioni standard.
Ogni materiale ha una sua temperatura caratteristica oltre la quale continua a bruciare e sotto la quale, invece, tende a esaurirsi, la cosiddetta temperatura di accensione.
(2) I comburenti sono tutte quelle sostanze in grado di ossidare i materiali combustibili, il più comune è l’ossigeno contenuto nell’aria. Altre sostanze ossidanti, sia liquide che solide o gassose che permettono la combustione, sono il nitrato di potassio, il permanganato di potassio, l’acqua ossigenata, il cromato di potassio e il protossido di azoto.
(3) Le fonti di innesco sono quelle fonti di calore necessarie a innalzare la temperatura del combustibile durante il processo di combustione. Si suddividono in: innesco per attrito, innesco diretto e innesco indiretto. Innesco per attrito, ossia quando il calore è prodotto dallo sfregamento di due materiali; innesco diretto, quando una fiamma, una scintilla o altro materiale incandescente entra in contatto con un materiale combustibile in presenza di ossigeno; innesco indiretto quando il calore di innesco si trasmette per convezione (quando la trasmissione del calore è accompagnata da un movimento di materia), conduzione (quando la propagazione del calore avviene attraverso elementi solidi) o irraggiamento (quando l'energia si propaga direttamente sotto forma di onde elettromagnetiche).
Il "triangolo" del fuoco
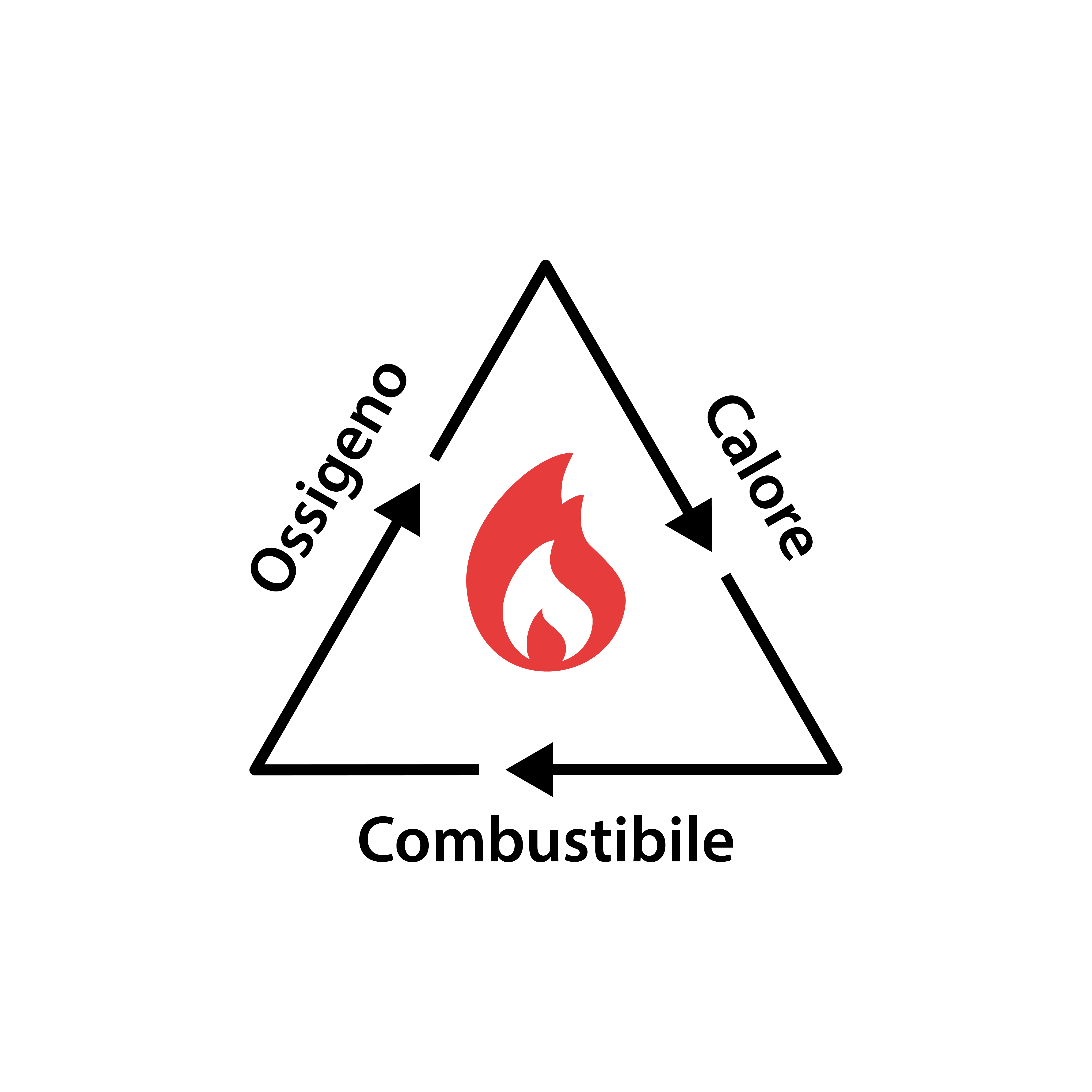
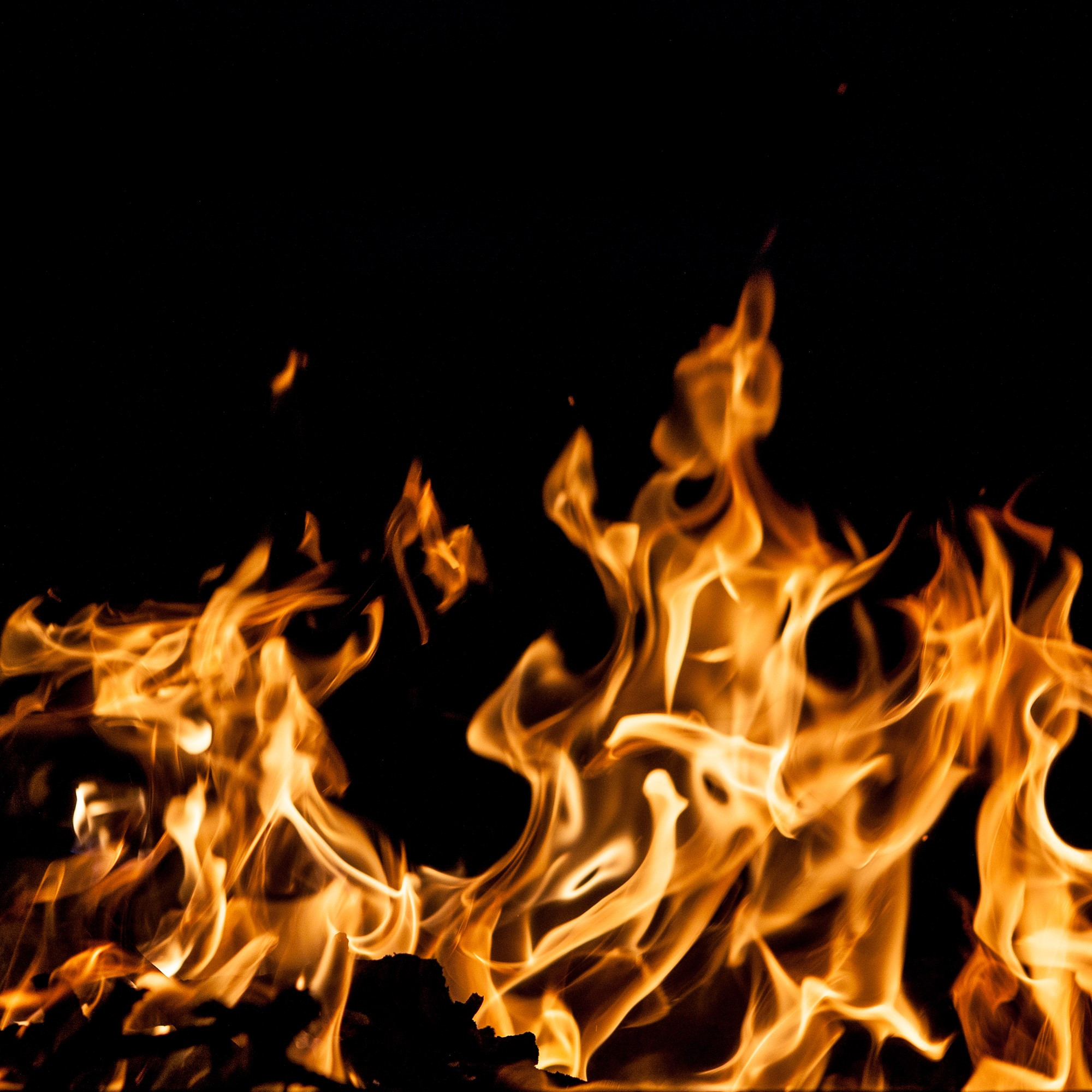
Ogni incendio è caratterizzato da quattro fasi distinte: ignizione e prima propagazione, flashover, incendio generalizzato e decadimento.
1 - Ignizione
in questa fase ha inizio il processo di combustione per effetto di una sorgente termica che riscalda il combustibile fino a portarlo alla sua temperatura di ignizione. Il propagarsi di questo fenomeno richiede necessariamente la presenza contemporanea dei tre elementi descritti nel
precedente paragrafo e riportati di seguito come lati di un ipotetico “triangolo" del fuoco. In assenza anche solo di uno dei fattori, l’innesco, e quindi l’incendio, non può avvenire. L’interruzione del triangolo del fuoco comporta lo spegnimento dell’incendio. Questa operazione può essere effettuata su ognuno dei tre lati, assumendo diversa denominazione a seconda del componente interessato: separazione (se si sottrae all’incendio il combustibile), soffocamento (se si impedisce il contatto tra l’aria o l’ossigeno e il combustibile), raffreddamento (se si abbassa la temperatura al di sotto di quella di accensione delle sostanze).
In questa fase se l’oggetto combustibile acceso è distante da altro materiale combustibile, il fuoco non si può propagare e, una volta esaurito il combustibile, la combustione cessa. Se, invece, nel suo cammino il combustibile acceso viene a contatto con altro materiale combustibile, per effetto di pirolisi, si possono generare vapori e gas facilmente accendibili; le
fiamme propagano l’incendio ai vari elementi combustibili e quindi, per gradi, a tutto il locale.
2 - Flashover
In questa fase, definita anche “punto di flashover”, la velocità di combustione si innalza, la temperatura aumenta e vengono prodotti rilevanti volumi di fumi e gas con propagazione improvvisa delle fiamme attraverso gas e vapori incombusti. È uno stadio di transizione da un incendio in crescita a uno pienamente sviluppato dove tutti i materiali combustibili sono coinvolti simultaneamente nell’incendio. Generalmente
questa fase comporta un incremento della temperatura sino a 500/600° in poco tempo (da 5 a 25 min).
3 - Incendio generalizzato
Al di sopra delle temperature di flashover la maggior parte dei materiali comuni è infiammabile e partecipa alla combustione. La trasmissione di calore all’interno degli edifici diventa rilevante e la resistenza strutturale di pareti, soffitti, pilastri e travi può essere seriamente compromessa. I rischi di
deterioramento e collasso delle strutture portanti da un lato e la rapidità di diffusione dell’incendio dall’altro, rendono questa fase particolarmente insidiosa.
4 - Decadimento
Il progressivo esaurimento del combustibile inizia un processo di estinzione con graduale riduzione del flusso di calore generato: è la fase del decadimento. In questa fase il raffreddamento è lento e ugualmente pericoloso: zone apparentemente fredde possono celare fuoco latente che aspetta “nuova benzina” per poter dar luogo a una nuova ignizione. Questa fase termina convenzionalmente quando la temperatura scende al di sotto
dei 300°C circa.
La “Prevenzione Incendi”, nel senso più ampio del termine, è la disciplina che studia e attua tutte le misure intese a prevenire, segnalare e ridurre la probabilità di insorgenza di un incendio e a limitarne le conseguenze per persone, cose, attività produttive e ambiente.
Come si può dedurre da questa definizione e dal seguito del testo, l’ambito della prevenzione include oltre alle misure di protezione antincendio, anche tutte le attività di formazione su rischi e comportamenti da tenere in caso di pianificazione di una strategia antincendio.
Per ridurre al minimo il rischio incendi, occorre infatti un’adeguata conoscenza dei rischi connessi all’utilizzo di determinati materiali (es. potere calorifico specifico) delle possibilità di separazione fisica di ambienti a elevato rischio incendio (anche tenendo conto delle possibilità di dislocazione dei locali in fase progettuale), delle norme e dei sistemi disponibili per ottenere un determinato grado di protezione.
La “protezione antincendio” poggia le basi su un complesso di misure finalizzate alla riduzione dei rischi e danni provocati dal sorgere di un incendio (danni alle persone, alle strutture, alle attività e all’ambiente) agendo sulla magnitudo dell’evento incendio (Rischio = Frequenza x Magnitudo).
E’ bene considerare tale definizione come estremamente generale, in quanto applicabile a qualsiasi tipo di attività o tipologia costruttiva: un edificio, un’industria, una galleria (stradale o ferroviaria) o un deposito di materiali.
E’ importante bilanciare in modo corretto misure di prevenzione e misure di protezione attiva e passiva, al fine di mitigare il rischio incendio e salvaguardare vita, beni e ambiente.
Uno degli obiettivi più importanti della protezione passiva al sufficiente a garantire la fuga di tutti gli occupanti e l’eventuale azione di estinzione incendio ad opera di squadre di soccorso o sistemi automatizzati.
Questa necessità è in caso di incendio messa a rischio dalle alte temperature che alterano le proprietà meccaniche (resistenza e rigidezza) delle strutture portanti con conseguente diminuzione della loro capacità di reggere carichi rispetto a condizioni di esercizio ordinarie.
Al fine di valutare il grado di resistenza di una struttura portante, la normativa Europea utilizza la variabile “R” (stabilità) seguita da un numero che indica in minuti il tempo per cui tale struttura è in grado di sostenere carichi in condizioni di incendio normalizzato (valutato secondo la curva ISO 834). Una parete o un pilastro con performance “R90”, ad esempio, sono certificati per esercitare la loro capacità portante per almeno 90 minuti di incendio. Accanto a impedire collassi strutturali, le misure di protezione passiva mirano a impedire che l’incendio si diffonda al di fuori del suo luogo di origine. Un rischio amplificato nel caso di edifici aventi occupanti con ridotte capacità psico-motorie o in caso di costruzioni alte in cui il percorso di fuga (“via di esodo”) dai piani superiori è spesso unico e deve essere tenuto libero da fiamme, fumi e gas di combustione.
Per far fronte al rischio di propagazione incendio la normativa prevede la suddivisione degli edifici in compartimenti, ovvero in aree di minore dimensione, il cui perimetro deve garantire “un sufficiente isolamento termico ed una sufficiente tenuta ai fumi e ai gas caldi della combustione”.
Ecco quindi che nel caso di elementi aventi sia funzione divisoria che strutturale (es. pareti e solai) accanto alla variabile R si aggiungono le variabili “E” per indicare integrità / tenuta a fiamme e gas caldi ed “I” per indicare l’isolamento termico (Tabella 1).
La tenuta è possibile solo se il supporto resta integro durante la prova. Qualsiasi sbrecciatura o cedimento anche puntuale nel supporto comprometterebbe non solo la possibilità di infiltrazioni ma anche l’isolamento termico della barriera. In fase di test il controllo è effettuato visivamente e con l’ausilio di un batuffolo di cotone che viene appoggiato sul punto più critico (es. la parte sporgente di una tubazione combustibile in attraversamento). L’accensione e permanenza della fiamma sul cotone, anche in assenza di evidenti collassi nel supporto, determina la fine della prova. L’isolamento termico è misurato attraverso l’applicazione di termocoppie in determinati punti critici del campione stabiliti convenzionalmente dalle norme di prova. Per una realizzazione di successo, la temperatura rilevata sul lato “freddo” non deve alzarsi in media più di 140°C rispetto alla temperatura ambiente e nessuna delle termocoppie deve misurare una differenza superiore ai 180°C.
L’unione dei requisiti di stabilità, tenuta e isolamento è indicato con l’acronimo “REI” che - seguito dal numero di minuti per cui tali proprietà devono essere mantenute - caratterizza le performance di resistenza al fuoco degli elementi di separazione portanti.
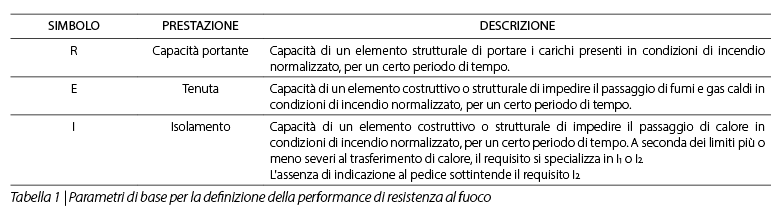
Protezione strutturale
Ai fini di una classificazione rilevante per gli obiettivi perseguiti dalla protezione passiva possiamo distinguere tre tipi di strutture:
- Strutture semplici
Elementi non continui (es. travi, pilastri, tiranti, catene), aventi pura funzione di sostegno meccanico. La mancanza di una funzione divisoria rende possibile caratterizzare la funzione antincendio di queste strutture soltanto attraverso la loro stabilità “R”. Al fine di misurare correttamente tale requisito è fondamentale che nei test siano inclusi carichi rappresentativi degli effettivi pesi che tali elementi dovranno sostenere. Nel caso si tratti di elementi sospesi (es. un tirante) è inoltre opportuno che i protettivi utilizzati siano anch’essi indipendentemente sostenuti o relativamente “leggeri” per poter contenere il surriscaldamento da incendio senza gravare troppo sull’elemento stesso.
- Strutture di separazione verticale portanti
Pareti di sostegno tipicamente realizzati in muratura, cemento armato e calcestruzzo, ma anche, più raramente in legno e pannelli compositi o misti.
- Elementi di separazione orizzontali
Solai ed elementi di copertura oltre ad essere elementi di separazione devono sostenere altri tipi di carichi quali mobili, persone e macchinari, che possono potenzialmente muoversi e variare la concentrazione nello spazio durante la vita utile dell’edificio. Accanto a tali carichi l’esposizione all’esterno potrebbe aggiungere sollecitazioni addizionali arrecate da agenti atmosferici (neve e vento) o altri carichi specifici (es. antenne di telecomunicazione, mezzi di trasporto etc…). Per questi fattori specifici qualunque test di resistenza deve essere contestualizzato con l’ausilio di valutazioni tecniche specifiche che tengano conto di questi elementi.
Per tutte le strutture sopra considerate, generalmente a maggiori spessori e densità corrispondono migliori performance e conseguentemente l’applicabilità dei risultati di test eseguiti su supporti con dati valori di densità e spessore sono automaticamente estesi a strutture dello stesso tipo con valori di questi parametri più alti. Al fine di migliorare i requisiti di resistenza meccanica di queste strutture si possono applicare intonaci, vernici intumescenti o rivestimenti in lastre di cartongesso/calcio silicato che, diminuendo il passaggio di calore aumentano l’isolamento e le performance R e REI dell’elemento portante o di separazione.
In caso d’incendio è fondamentale evitare la propagazione delle fiamme all’intero edificio. Il compartimento individua la zona nella quale deve rimanere relegato l’incendio, nel caso non sia previsto, o non sia necessaria alcuna compartimentazione, l’edificio coincide con il compartimento.
Gli elementi di separazione orizzontale e verticale che definiscono il perimetro dei compartimenti - come visto in precedenza - devono garantire per un certo arco temporale una performance di tenuta ai fumi (indicata con la lettera “E”) e di isolamento termico (indicata con la lettera “I”).
Al fine di accertare queste proprietà, pareti e solai analoghi a quelli utilizzati nelle costruzioni devono aver superato test di resistenza al fuoco secondo gli standard Europei EN 1364 ed EN 1365 ed aver ottenuto una classificazione su queste due proprietà migliore o uguale a quella richiesta agli elementi impiegati nel progetto reale. In alternativa è possibile dimostrare che tali elementi rispondono alle caratteristiche tabellari del D.M 16 febbraio 2007 (allegato “D”). Nel caso siano presenti delle discontinuità su pareti e solai (porte, serrande, attraversamenti di impianti o giunti lineari) che riducono lo spessore isolante o cambiano la natura stessa dei materiali impiegati per garantire integrità e isolamento termico, le certificazioni ottenute sugli elementi di separazione semplici non sono più sufficienti ed è necessario che l’installazione sia supportata da certificati realizzati su elementi omogenei a quelli impiegati in cantiere.
In particolare ciascun elemento utilizzato per ripristinare la continuità dell’integrità e dell’isolamento termico agisce con modalità differenti a seconda della natura della discontinuità e deve essere applicato seguendo le indicazioni di posa riportate nelle schede fornite dal produttore.
L’intervento non è puntuale e slegato dalla costruzione di supporto, bensì deve essere considerato nel suo complesso ed effettuato con tutte le accortezze e gli eventuali prodotti complementari utilizzati in prova: non si certifica l’idoneità di una porta o di un vetro antifuoco senza testare il supporto in cui tali elementi sono inseriti e i prodotti accessori eventualmente utilizzati per garantire una perfetta sigillatura. Questa necessità di analizzare l’elemento di discontinuità nel contesto in cui è inserito enfatizza l’importanza delle modalità di posa in opera e porta a prediligere il concetto di “sistemi” antifuoco, su quello di prodotti antifuoco.
Di seguito presentiamo i principali sistemi utilizzati per realizzare una compartimentazione antincendio su supporti che presentino discontinuità.
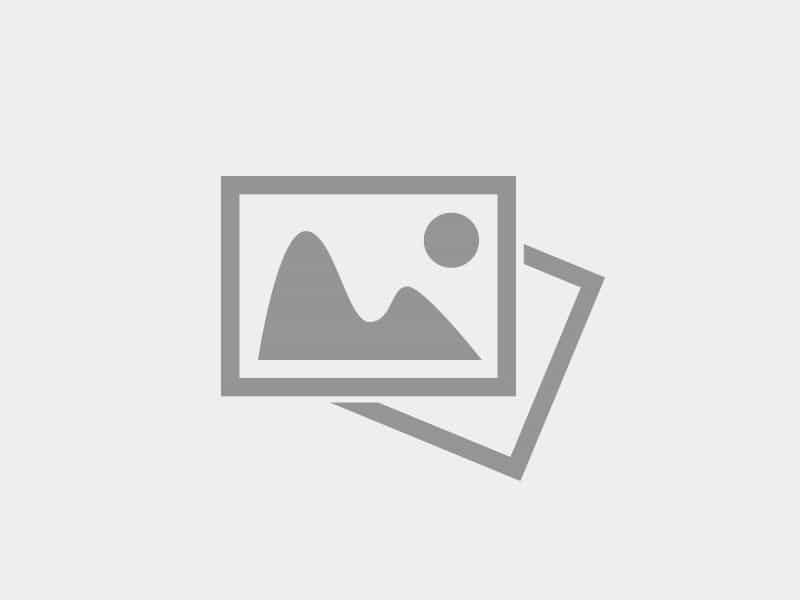.jpg)
Iniziamo questo breve excursus sulle chiusure e sigillature tecniche parlando delle porte resistenti al fuoco, note comunemente come “porte REI”. Questo tipo di chiusura è regolamentato da standard di prodotto e dal novembre 2019, il termine del periodo di coesistenza della norma armonizzata ha reso obbligatoria la marcatura CE. Per la precisione, alla data di scrittura di questo testo, solo per le porte esterne pedonali o carrabili (EN 14351-1) è obbligatoria la marcatura CE, mentre per le porte pedonali interne (EN 14351-2) vige ancora la necessità della omologazione nazionale; ciascuno Stato membro si muove quindi in autonomia. Indipendentemente dagli sviluppi certificativi c’è da sottolineare che, oltre alla modifica delle procedure di prova, è stato introdotto il concetto di tenuta ai fumi anche per le porte e cancelli industriali, ciò comporta il fatto che, durante la prova, si effettuano le misurazioni di tenuta a temperatura ambiente (20°C) per le porte di tipo Sa, e a una temperatura intermedia (doppia misurazione, a 20°C e a 200°C) per le porte di tipo Sm. Pertanto la classificazione caratterizzante può essere di tipo “E”, “EI” e “EW” (non più “REI”), con i suffissi “-Sa“ oppure “-Sm”. Le porte tagliafuoco possono essere soggette a usura o malfunzionamento e proprio per questa motivazione si deve procedere alla manutenzione semestrale.Porte Tagliafuoco
Attraversamenti di impianti
Gli attraversamenti di impianti tecnici, per tipologia e numerosità, costituiscono probabilmente la minaccia più forte alla tenuta delle misure di compartimentazione. Si tratta di una categoria molto ampia che tuttavia presenta degli elementi comuni. Ciascuna riqualificazione di attraversamenti è in particolare definita da tre fattori:
- servizi passanti;
- supporto costruttivo;
- prodotti impiegati.
Al fine di valutare (e di comparare) diverse soluzioni è necessario considerare ciascuno di questi tre punti. Come ben noto la certificazione della resistenza al fuoco dei sigillanti posati in opera da un professionista antincendio deve basarsi su rapporti di classificazione o benestare tecnici (ETA) che abbiano nel loro campo di applicazione diretta (o estesa in base alle indicazioni delle normative EXAP) il caso reale di cantiere; non sono consentite estensioni o valutazioni nemmeno da parte di un tecnico sebbene abilitato e iscritto all’Albo presso il Ministero dell’Interno. Questa condizione comporta una sfida per le aziende produttrici di sistemi di sigillatura antifuoco perché ogni cambiamento rilevante che riguardi la costituzione dei servizi passanti, dei supporti costruttivi o dei prodotti utilizzati richiede potenzialmente un test dedicato, aumentando il numero di certificazioni necessarie a coprire un ambito applicativo.
Esiste un unico criterio di base che viene recepito da tutte normative che regolano gli attraversamenti di impianti (EN 1366) per l’estensione dei risultati di prova: i risultati ottenuti in condizioni peggiorative possono essere considerati validi ed estesi ad attraversamenti che presentino condizioni analoghe o migliorative dal punto di vista della capacità di tenuta e isolamento termico. Il certificato di un collare testato su una parete di cartongesso di spessore 120 mm sarà ad esempio estendibile a un’applicazione su una parete rigido con spessore 150 mm, mentre non sarà possibile effettuare l’estensione nell’altro senso. Da questa condizione nasce la spinta per le ditte fabbricanti a provare i propri sistemi nelle situazioni più gravose con l’intento di estendere il campo di applicazione delle proprie soluzioni. Vediamo di seguito più nel dettaglio come questo criterio si applica per ciascuno dei tre elementi che definiscono un attraversamento.
La tipologia e configurazione di installazione degli elementi che attraversano pareti e solai è il primo degli elementi di differenza tra attraversamenti. Riconoscere la “tipologia” o natura di un servizio è immediato: un cavo è diverso da un tubo e un tubo combustibile di piccolo diametro è diverso da un tubo metallico di grandi dimensioni. L’importanza della tipologia dell’elemento passante è tale che nei paragrafi successivi useremo proprio questo criterio come base per suddividere l’esposizione delle particolarità di ciascun attraversamento. Meno banale ma altrettanto importante è la configurazione di installazione dei servizi ovvero l’insieme di tutti i dettagli costruttivi che sono stati utilizzati per certificare l’attraversamento in fase di test. Queste condizioni al contorno sono una parte integrante della soluzione non sempre facile da replicare o verificare al di fuori dei laboratori specializzati. Nella realtà sono possibili delle varianti ad una configurazione di test purché l’elemento provato in laboratorio presenti un allestimento più gravoso di quello reale dal punto di vista del comportamento in caso di incendio. Un caso particolarmente rilevante a questo proposito è la presenza e lo spessore di eventuali cornici intorno all’attraversamento che aumentino localmente lo spessore del supporto e conseguentemente la profondità del sigillante.
Per fare un po’ di chiarezza vediamo un esempio pratico: il perimetro di un’apertura delimitato da una cornice. Se nel rapporto di prova è stata utilizzata una cornice dove alloggiare e installare il sigillante, la stessa deve essere costruita anche in cantiere. Molte volte si omette la costruzione dei supporti aggiuntivi per praticità o per motivi di risparmio economico; la norma dei test di resistenza al fuoco degli attraversamenti di servizi (EN 1366-3) non prevede tuttavia questa possibilità in quanto il sistema sarebbe stato provato in laboratorio in condizioni meno gravose (con l’ausilio di una cornice per l’appunto) del caso reale e non vi è quindi alcuna garanzia sul suo funzionamento senza tali sostegni perimetrali. Ciò implica per molti dei sistemi disponibili sul mercato, una limitazione di applicabilità alla sola versione con cornice (vedi immagine sotto). Se al contrario il test ha utilizzato un varco tamponato con il solo sigillante antincendio senza alcuna costruzione aggiuntiva come in Figura 3a (condizione peggiorativa), è possibile applicare i prodotti di sigillatura in entrambe le configurazioni, ovvero sia con che senza cornice (vedi Figure 3b e 3c).
L’assenza in fase di test di configurazioni di installazione difficili da realizzare in cantiere è uno degli elementi più importanti per assicurare la conformità dei sistemi installati a quanto certificato. E in questa direzione sono andati gli sforzi di Ricerca e Sviluppo di AF Systems degli ultimi anni. È importante che il tecnico antincendio, non avendo alcuna facoltà di estendere e/o validare una modifica al sistema di installazione, analizzi approfonditamente la soluzione proposta tenendo presente tutte le condizioni al contorno presenti sui certificati.
Figura 3a
Soluzione AF Systems senza cornice
Figura 3b
Soluzione con cornice esterna
Figura 3c
Soluzione con cornice interna
La norma distingue tra due tipologie: parete/solaio flessibile (costruzione a secco o in legno) e parete/solaio rigido (muratura, calcestruzzo...). Fermo restando l’impossibilità di estendere i risultati ottenuti su supporto orizzontale a un supporto verticale e viceversa; è importante sapere che per essere conforme al certificato, il supporto reale deve avere uno spessore e una densità maggiori, o uguali, a quelli testati. Nella prova le aziende produttrici puntano a utilizzare pareti (o solai) con lo spessore e la densità minori possibile, al fine di garantire la massima estendibilità dei risultati.
Inoltre, la norma concede di estendere i risultati ottenuti su un supporto flessibile anche a un supporto rigido, purché quest’ultimo abbia uno spessore maggiore o uguale a quello della parete (o solaio) di prova. Oltre alle pareti e solai standard (cartongesso, muratura o calcestruzzo) vengono utilizzate di frequente partizioni che non rientrano nel campo di applicabilità o estensione: stiamo parlando di supporti realizzati con pannelli sandwich e/o setti autoportanti (in cartongesso o silicato). Per poter applicare sistemi di sigillatura in questi casi è necessario utilizzare sistemi appositamente certificati su tali supporti.
Riportiamo queste indicazioni nella Tabella 2 sottostante in cui si confronta l’elemento certificato con il campo di applicazione dello stesso.
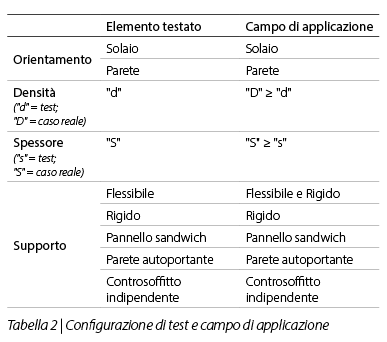
I sistemi di sigillatura possono comprendere uno o più prodotti. Nella maggior parte dei casi un prodotto principale si accompagna a prodotti complementari, il cui utilizzo è indispensabile al fine di ottenere determinate performance. Un esempio classico di utilizzo di prodotti complementari è presente nei casi in cui vi è un’apertura (nel seguito di questo catalogo denominata anche “asola”) di dimensioni molto superiori a quelle dell’elemento passante. In queste situazioni accanto al prodotto principale (es. un collare intumescente) si utilizzano prodotti complementari che ricostituiscono la continuità del supporto intorno all’attraversamento (es. pannelli in lana minerale o mattoncini e schiume intumescenti).
Dal punto di vista dell’utilizzatore finale, nella maggior parte dei casi, la preferenza è per sistemi che impieghino il minor numero di prodotti diversi possibili. Il numero ridotto di articoli ha un duplice vantaggio: da un lato tende a diminuire il costo di posa e facilitare la quantificazione degli approvvigionamenti, dall’altro un minor numero di prodotti si accompagna generalmente a una maggiore facilità di posa e di realizzazione di una sigillatura conforme a quanto certificato.
Accanto alla varietà di prodotti utilizzati è utile verificare la quantità necessaria, e più precisamente, la profondità di sigillatura richiesta dalla configurazione testata. Una minore profondità di sigillatura permette ovviamente risparmi in fase di acquisto e in molti casi è anche un fattore vincolante per la possibilità di utilizzare il sistema. Come abbiamo visto nella sezione “Servizi passanti” spessori di sigillante ridotti permettono di applicare la soluzione anche a pareti e solai di ridotto spessore senza necessità di aumentare localmente lo spessore degli stessi con cornici o altri sistemi.
Per capire in modo concreto quanto numerosità dei prodotti e profondità di sigillatura siano uno strumento potente di confronto tra diverse soluzioni, si consideri un caso concreto ovvero un attraversamento di cavi disposti su passerelle, sigillato con sacchetti intumescenti.
Nel BOX 2 si vedono tre attraversamenti identici sigillati con tre diversi sistemi per il conseguimento di una performance EI 120.
Le condotte d’aria rappresentano un canale naturale di propagazione dell’incendio e per questo devono essere accuratamente protette al fine di garantire tenuta e isolamento termico tra compartimenti adiacenti. Il punto critico è ovviamente rappresentato dall’attraversamento e i metodi impiegati secondo la norma EN 1366-1 si concentrano su questo punto prevedendo un tamponamento di tutta l’area intorno alla condotta con materiali ad alta capacità isolante (es. pannelli in lana minerale). La dimensione e la conduttività dei canali metallici è tuttavia tale che una protezione localizzata solo in corrispondenza degli attraversamenti non è sufficiente ad abbassare le temperature ai livelli richiesti dalla normativa.
Per questa ragione i sistemi in commercio prevedono il rivestimento completo della condotta con materiali altamente isolanti: materassini flessibili, lastre a base gesso o silicati o intonaci. Questa necessità di un rivestimento lungo tutta la condotta ha spesso generato nel mercato l’equivoco che la normativa richiedesse una resistenza meccanica e/o l’isolamento termico continuo, della condotta. Non è così. La norma EN 1366-1 è infatti una norma di riqualificazione degli attraversamenti il cui obiettivo non è dare un grado di protezione dal fuoco all’intera linea ma garantire la tenuta del compartimento. L’evidenza di questo concetto è riscontrabile nei risultati presenti nei rapporti di classificazione che si concentrano sulle prestazioni del sistema in corrispondenza dell’attraversamento: un sistema con performance EI 120 è correttamente protetto, se sul lato “freddo” dopo 120 minuti di incendio, secondo la curva ISO 834 (vedi paragrafi precedenti), la temperatura non è aumentata in media più di 140 °C o in un singolo punto di 180°C, né si sono verificate infiltrazioni di fumi o gas di combustione. Non tutte le condotte sono uguali. La caratteristica più importante certificata è la presenza o meno del fuoco all’interno della condotta. Per questo la norma EN 1366-1 prevede due diverse configurazioni di test: condotta con fuoco esterno in attraversamento (condotta di tipo A, con classificazione [o→i]) e condotta con fuoco interno in attraversamento (condotta di tipo B, con classificazione [o←i]).
Figura 4a | Profondità di sigillatura 120 mm
Il primo sistema, il nostro “caso base”, utilizza i
cuscinetti AF Bags certificati con il lato “corto” di 120 mm disposto parallelamente allo spessore del supporto; è quindi disponibile il lato più lungo degli stessi di 300 mm per occludere la sezione dell’attraversamento. Il numero di unità necessarie a tamponare il varco è conseguentemente ottimizzato. Dal momento
che non è stata impiegata in fase di test, non è
necessario predisporre una cornice esterna per
omologare l’installazione a quella certificata.
Figura 4b | Profondità di sigillatura 320 mm
Il secondo sistema è a differenza del primo
certificato con cuscinetti che utilizzano il loro lato “lungo” di 320 mm disposto parallelamente allo spessore del supporto e il lato “corto” di 200 mm per occludere la sezione dell’attraversamento. Il numero dei sacchetti necessari per la sigillatura è conseguentemente ca. il 65-70% più alto rispetto al nostro caso base. Inoltre risulta necessario aggiungere una cornice di profondità 250 mm per un’installazione certificata.
Figura 4c | Profondità di sigillatura 600 mm
Il sistema è certificato come nel secondo caso
con il lato “lungo” – in questo caso di 300 mm
- disposto parallelamente allo spessore del
supporto e con l’aggiunta di sacchetti su entrambi i lati dell’attraversamento per una profondità di sigillatura di 150 mm aggiuntivi su ogni lato in corrispondenza delle passerelle. La combinazione di questi due fattori aumenta molto il numero di unità necessarie per realizzare una sigillatura conforme, portando il numero totale di cuscinetti a essere più che doppio rispetto al caso base. Necessaria l’aggiunta di una cornice.
Figura 5 | Schemi di prova condotte d'aria secondo la EN 1366-1
a. Condotta di tipo A (fuoco esterno)
b. Condotta di tipo B (fuoco interno)
c. Tamponamento tagliafuoco
d. Isolamento
e.. Aperture
Un’alternativa per la protezione degli attraversamenti delle condotte d’aria è rappresentata dalla possibilità di inserire all’interno delle pareti/solai di delimitazione dei compartimenti, degli elementi tagliafuoco che creino un disaccoppiamento tra il tratto di condotta presente in un compartimento e quello adiacente.
La normativa di riferimento, la EN 1366-2, è utilizzata per testare le caratteristiche di questi sistemi denominati serrande tagliafuoco. Per questi dispositivi esiste una norma di prodotto e di conseguenza l’obbligo di marcatura CE. Il funzionamento di questi meccanismi consiste nell’interrompere il condotto in corrispondenza della partizione resistente al fuoco per mezzo di una pala in silicato (o materiale equivalente). Le serrande tagliafuoco si utilizzano solo in quei casi in cui è consentito bloccare il flusso dell’aria in caso di incendio. La norma descrive anche i criteri di installazione; si possono installare su muratura o su parete flessibile seguendo le procedure schematizzate per ciascuna configurazione, fermo restando l’obbligatorietà di non applicare la serranda su un supporto diverso da quello testato. La sigillatura del perimetro attorno alla serranda deve essere eseguito con le metodologie indicate nella scheda del prodotto; nel caso si preveda l’utilizzo esternamente alla costruzione di supporto (disassamento) si deve provare anche il caso scelto.
Gli attraversamenti di cavi elettrici costituiscono uno dei punti più critici per la compartimentazione degli edifici a causa dell’elevato rischio di innesco incendio che li caratterizza. Cortocircuiti e sovraccarichi di corrente, guasti ai conduttori o ai terminali di collegamento possono generare un forte surriscaldamento e logorare o “accendere” gli strati di isolamento dei cavi. I sistemi certificati secondo la norma EN 1366-3 riqualificano l’attraversamento proteggendo lo spazio libero intorno ai cavi e garantendo che in caso di incendio, fiamme e gas di combustione non passino da un compartimento all’altro. L’attraversamento di cavi elettrici, per la sua elevata criticità, deve sempre essere messo in sicurezza e anche in presenza di attraversamenti di dimensioni ridotte, non esiste alcuna normativa Europea che preveda eccezioni*. A livello normativo i cavi possono distinguersi sulla base della funzione in elettrici o di telecomunicazione sulla base della dimensione in piccoli, medi e grandi e sulla base della presenza o meno del rivestimento isolante. Nell’edilizia civile la stragrande maggioranza dei casi si concentra su cavi rivestiti di piccole dimensioni (diametro esterno inferiore o uguale a 21 mm). Tuttavia è importante verificare che il diametro del cavo di proprio interesse sia ricompreso negli intervalli testati e che raggiunga la resistenza al fuoco necessaria.
Dal punto di vista delle configurazioni di posa nella maggior parte dei casi, i cavi sono alloggiati all’interno di passerelle metalliche incombustibili ma possono anche essere collocati all’interno di tubazioni plastiche (generalmente tubi corrugati in PVC) o, in casi estremi, restare liberi senza alcun sistema di sostegno esterno. I sistemi di sigillatura a loro volta presentano una grande varietà con diversi gradi di flessibilità a seconda delle necessità previste di re-intervento a fini manutentivi e/o di realizzazione di varianti progettuali (es. inserimento di altri cavi). Le soluzioni più flessibili includono sacchetti e mattoncini intumescenti, facilmente rimovibili e ricollocabili, quelle intermedie o semirigide comprendono pannelli a bassa densità o schiume intumescenti bicomponenti facilmente perforabili e infine quelle più “rigide” prevedono la sigillatura completa del varco con malte cementizie. Le specifiche esigenze di manutenzione e/o variazione dell’impianto elettrico rendono molto rara l’adozione di sistemi rigidi e la gran parte dei sistemi di sigillatura antifuoco recentemente messi sul mercato (es. mattoncini tagliafuoco) sono facilmente rimovibili per facilitare successivi interventi sulla rete. Accanto ai requisiti di flessibilità, il parametro principale di differenziazione dei sistemi di sigillatura degli attraversamenti di cavi dal punto di vista dell’utilizzatore è costituito dalla profondità di sigillatura. Le soluzioni disponibili sul mercato offrono valori molto diversi: a partire da 120 mm (es. AF Bags in questo catalogo) fino a più di 300 mm. Ovviamente una minore profondità di sigillatura certificata è preferibile dal punto di vista della progettazione e dell’applicazione in quanto diminuiscono sia il rischio che lo spessore dell’isolante superi quello del supporto in cui è inserito che i costi complessivi dell’intervento.
* Nonostante ciò in alcuni Paesi, normative nazionali o mutuate dal codice elettrico vengono richiamate per escludere la necessità di protezione in caso di attraversamenti di ridotte dimensioni. Uno di questi esempi è costituito dalla normativa IEC 20-36/4-0 che tuttavia descrive esclusivamente i metodi di prova per la resistenza al fuoco di determinati cavi e non fa alcun cenno relativo alla norma di prova sugli attraversamenti.
La norma divide le tubazioni in due macro gruppi: combustibili e incombustibili. Tralasciando per un momento le specificità di ciascun gruppo sottolineiamo alcuni aspetti che risultano differenzianti in entrambi i gruppi, a partire dal diametro e dalle condizioni dell’estremità della tubazione. Consideriamo le tubazioni incombustibili: per avere un campo di applicazione valido la norma prevede di testare il diametro minimo (con lo spessore minore) e i diametri massimi (uno con lo spessore minore ed uno con lo spessore maggiore); si ottiene come risultato quindi un intervallo sia di diametri che di spessori.
Figura 6 | Esempio di grafico di copertura
Nel caso evidenziato in Figura 6 tutti i tubi compresi nell’area tratteggiata possono essere protetti. Risulta quindi interno al campo di applicazione un tubo con diametro 200 mm e spessore delle pareti pari a 8 mm mentre non risulta coperto da questa certificazione un tubo dello stesso diametro con spessore delle pareti pari a 4 mm. Questo esempio ci porta a comprendere il giusto valore del test effettuato sul punto “C” ovvero su un tubo con diametro 40 mm e spessore delle pareti pari a 3 mm. Grazie a questo test, il produttore ha esteso il campo di applicazione del proprio sistema a tubi di piccole dimensioni con spessore delle pareti più sottili di quelle dei tubi più grandi. Questo spessore minimo tuttavia non è automaticamente esteso a tutti i diametri, ma solo a quello che ricadono all’interno della figura soprastante.
Il discorso di cui sopra ovviamente si basa su una doverosa premessa ovvero che i sistemi protettivi testati per i punti “A”, “B” e “C” siano omogenei. Se pensiamo a dei collari, ad esempio, è necessario che spessore, altezza e consistenza della parte intumescente e della struttura metallica siano equivalenti per tutti i punti testati.
Riportiamo per completezza anche il grafico di copertura presente nella normativa EN 1366-3 relativo a tubazioni coibentate. In questo caso la complessità aumenta in quanto oltre ai doppi spessori delle pareti del tubo, per avere un adeguato campo di applicazione è necessario testare per gli stessi diametri anche tubi con diverso spessore dell’isolante.
Figura 7 | Grafico di copertura per tubazioni coibentate
I gradi di estendibilità dei risultati di prova sono indicati nella Tabella 3:
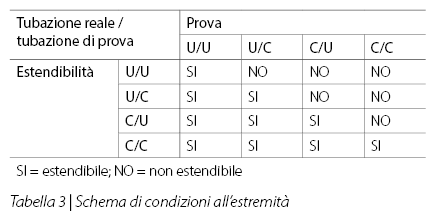
Le varie configurazioni corrispondono a servizi di tipo diverso e la norma li richiama in un’apposita tabella (vedi Tabella 4). Vediamo ora più nel dettaglio come la tipologia di materiale di cui sono costituite le tubazioni impatti sulla scelta del sistema protettivo da impiegare.Tubazioni combustibili (EN 1366-3)
Questo tipo di servizi perde di consistenza in un intervallo di temperature relativamente basse da 80-220°C. In pochi minuti il collasso della tubazione lascia nel supporto un’apertura esposta all’infiltrazione di fiamme, fumi e gas di combustione. Il compito primario di una barriera tagliafuoco è quello di ripristinare immediatamente l’integrità del supporto, chiudendo qualsiasi punto libero generato dalla sparizione degli elementi combustibili. Il sistema più utilizzato impiega la reazione chimica denominata “intumescenza”, ovvero la capacità di un materiale, contenuto all’interno del sigillante, di incrementare il proprio volume all'aumentare della temperatura. L’innesco di questo processo avviene generalmente a temperature attorno ai 180°C e continua fino alla temperatura di circa 400°C. È importante conoscere la natura del tecnopolimero perché ciascuna tipologia (PVC, PP, HDPE…) fonde e si comporta al fuoco in diversa maniera; la norma di prova ne tiene conto e impone test dedicati per le diverse tipologie; oltre a ciò impone anche di testare il comportamento del sigillante sulle tubazioni composite speciali delle diverse ditte produttrici.
A differenza della precedente tipologia, la maggior parte dei materiali “incombustibili” (es. ferro, acciaio e rame) fonde ad una temperatura superiore ai 1000°C e mantiene la propria integrità durante l’incendio. Al contrario, l’elevata conduttività porta velocemente i materiali a surriscaldarsi e diventare una possibile fonte di innesco incendio in altri compartimenti. Il focus dell’intervento si concentra quindi sull’isolamento termico con l’obiettivo di tenere freddo l’attraversamento attraverso il rivestimento con protettivi isolanti o rivestimenti ablativi.
Un caso particolare di rilievo è rappresentato dall'alluminio che, fondendo a temperature relativamente basse (circa 600°C), potrebbe non rimanere integro durante un incendio. Questa sensibile differenza di comportamento al fuoco rende il caso dei metalli che fondono a temperature inferiori ai 1000 °C molto critico e laddove i materiali isolanti non bastino a garantire temperature al di sotto del punto di fusione degli stessi, il sistema dovrà impiegare anche materiali intumescenti in grado di ripristinare l’integrità del supporto.
Nel caso in cui le tubazioni metalliche siano coibentate si deve tenere conto della natura dell’isolante. Se il coibente è di tipo combustibile, la tubazione è protetta con un prodotto termo-espansivo, ad esempio un collare o una striscia intumescente.
Il sistema di sigillatura può essere applicato direttamente sul rivestimento o previa rimozione e sostituzione dell’isolamento, a seconda delle modalità di uso certificate dal produttore. Dal punto di vista dell’applicazione il primo metodo è sicuramente meno dispendioso per l’applicatore e per questo all’interno della gamma di soluzioni AF Systems tutti i sistemi certificati non prevedono la necessità di sostituire l’isolamento (es. il collare si applica direttamente sulla coibentazione elastomerica). Nel caso in cui la coppella di rivestimento sia in una lana minerale incombustibile (classe A1 o A2) con temperature di fusioni superiori a quelle presenti nel forno di prova, l’isolante sinterizza ma non scompare: il punto critico è assicurare la tenuta della sigillatura lungo il perimetro di contatto tra lana minerale e supporto; un’azione che può essere effettuata sia attraverso elementi intumescenti che attraverso altri tipi di sigillanti ad esempio acrilici. La norma precisa inoltre che i risultati di test condotti con coppelle in lana di vetro con temperature di fusione relativamente basse, si possono estendere a quelle in lana di roccia; ma non viceversa.
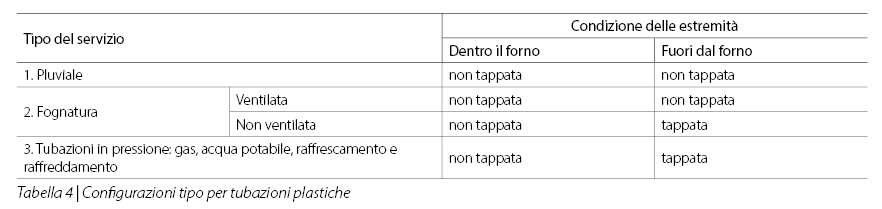
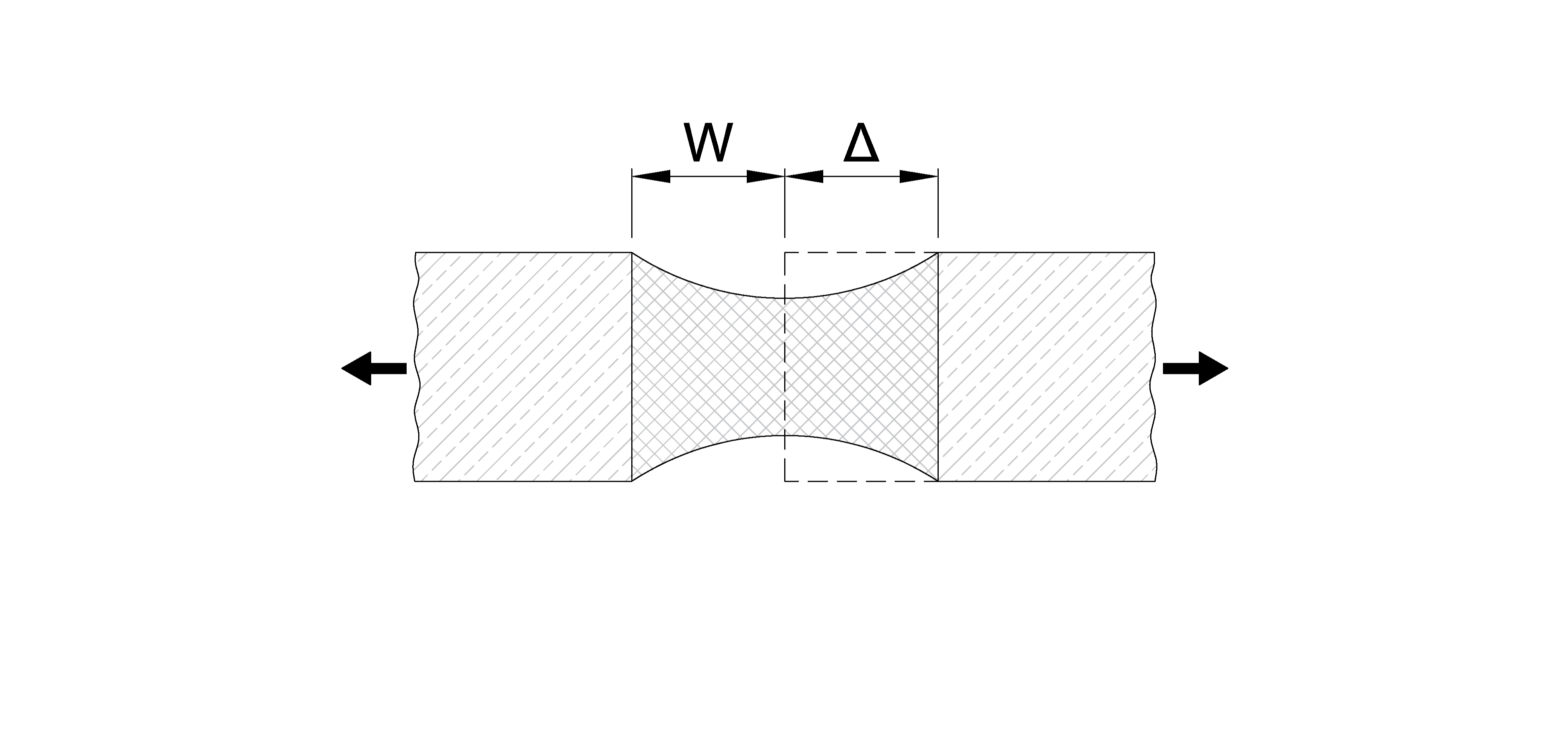
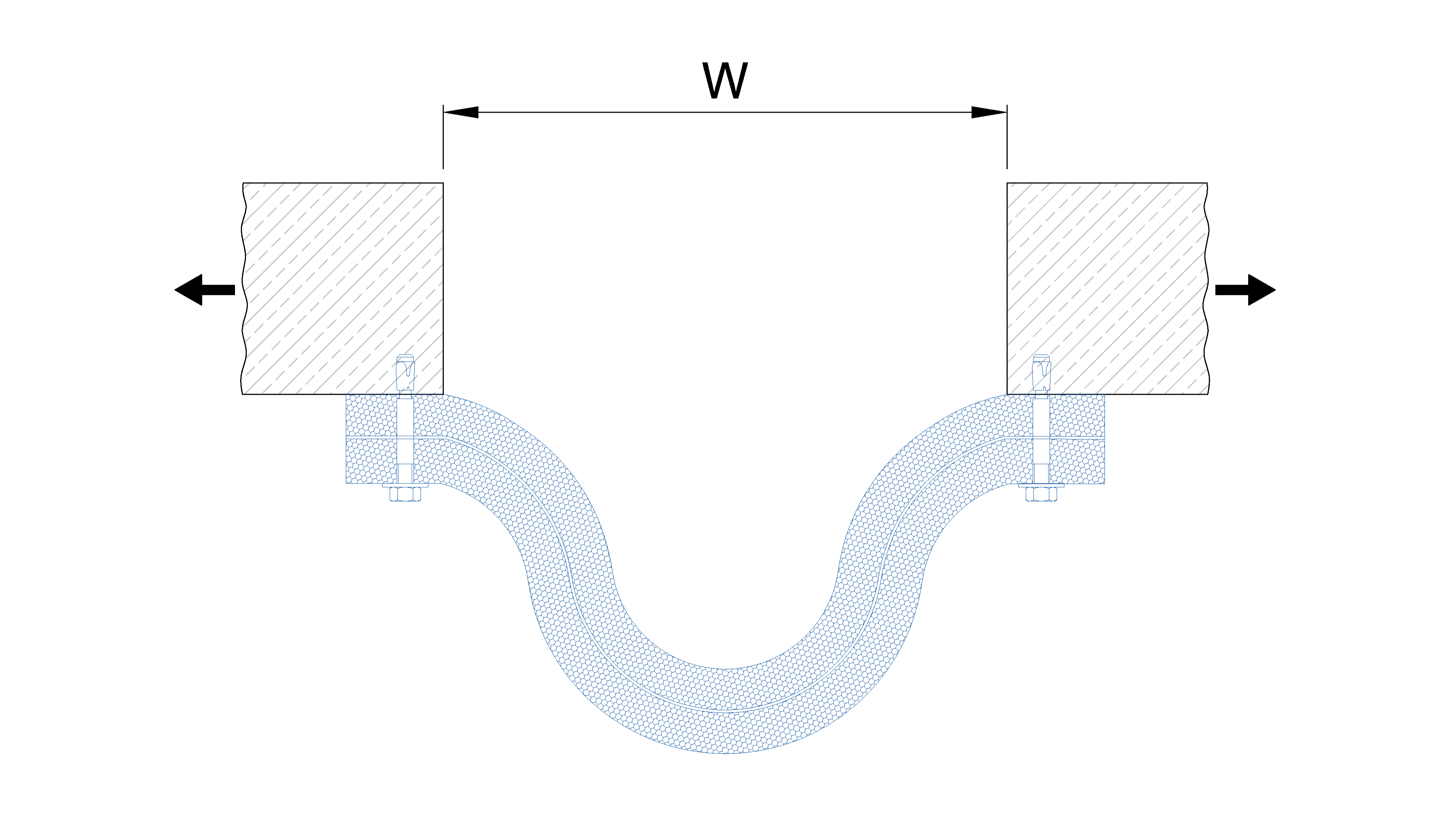
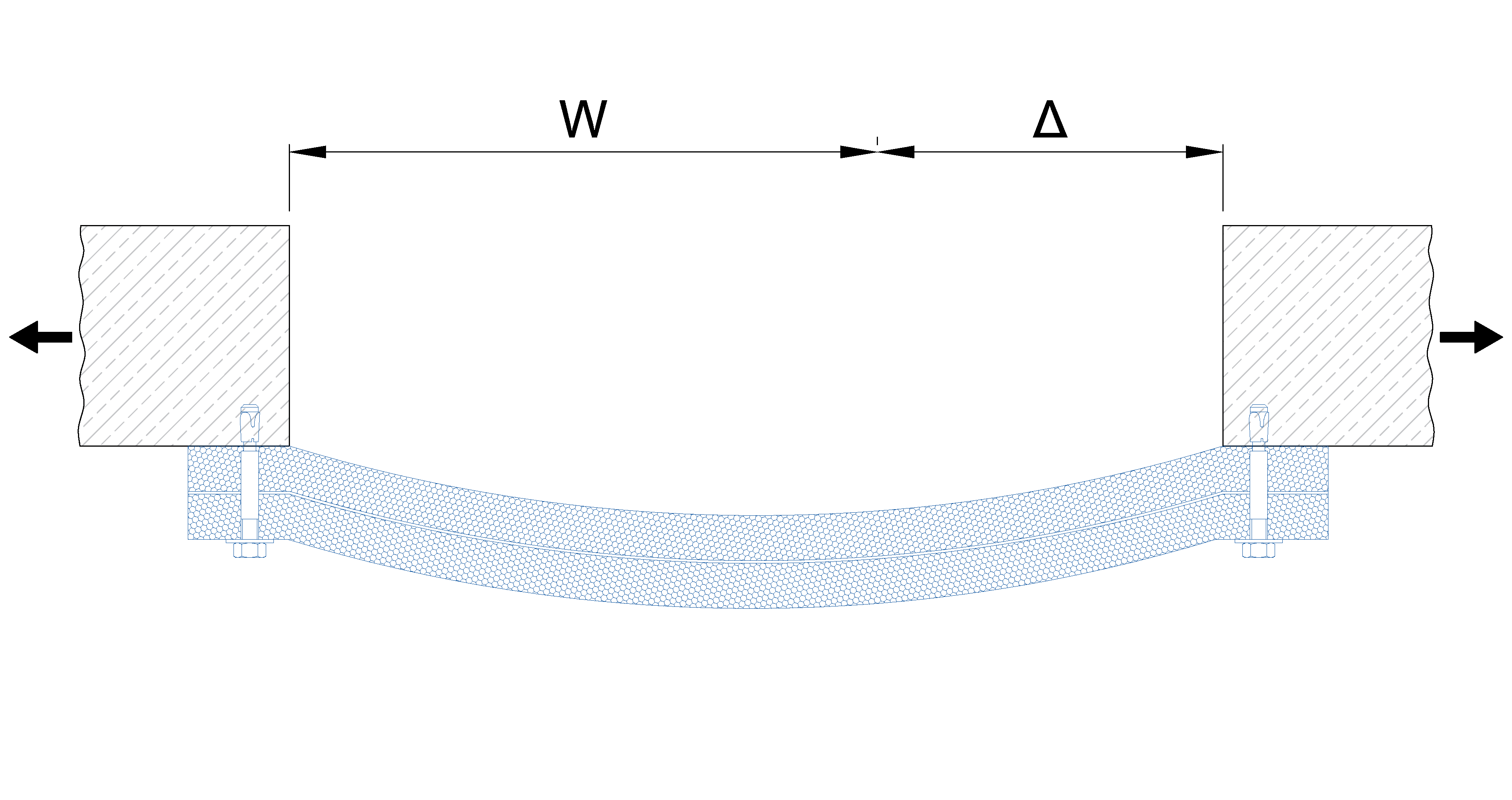
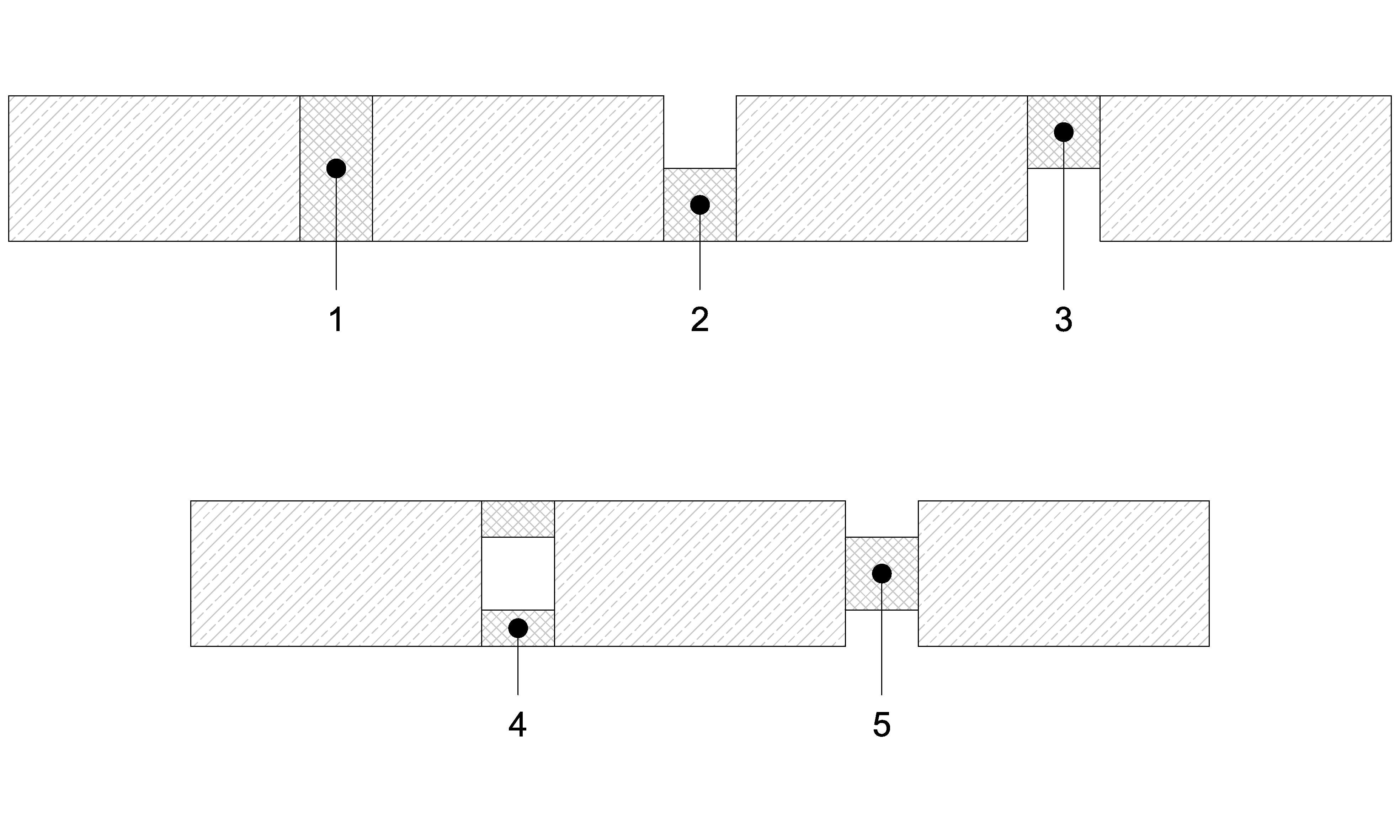
Per giunti lineari si intende una soluzione di continuità in
una parete o solaio che presenti un rapporto tra lunghezza
e larghezza di almeno 10:1. L’inserimento di queste aperture
in fase progettuale risponde nella maggior parte dei casi a
un’esigenza di flessibilità strutturale: questi spazi aperti sono
buffer che consentono che piccoli movimenti delle strutture
(dovuti ad esempio a dilatazioni termiche o vibrazioni del
terreno), non provochino crepe o rotture nei materiali stessi.
Si vede quindi come il giunto lineare sia un elemento di
tensione tra necessità di stabilità meccanica e necessità di
compartimentazione antincendio. Questa doppia necessità ha
determinato nella protezione passiva al fuoco la preferenza per
sistemi non completamente rigidi, che possano permettere un
certo grado di movimento delle strutture.
In particolare la normativa distingue due casi: i giunti senza
movimento, che possono essere sigillati per necessità di
compartimentazione con protettivi che possono comprimersi
ed espandersi fino al 7,5% dell’ampiezza nominale del giunto,
e i giunti con movimento che possono essere sigillati con
sistemi che possono comprimersi ed espandersi più del 7,5%.
Nel primo caso la norma di test (EN 1366-4) non prevede
una prova di movimento in aggiunta a quella di resistenza al
fuoco, mentre nel secondo caso dopo aver opportunamente
sigillato l’interstizio (e prima dell’inizio del test) si avvicinano e
allontanano le due parti della costruzione di supporto, al fine
di verificare la tenuta e isolamento del coprigiunto dopo una
condizione di stress meccanico.
In Paesi con frequente attività sismica (l’Italia ne è un esempio)
i movimenti strutturali legati alla normale attività tellurica,
portano a scegliere sistemi che permettano alle estremità dei
giunti di muoversi liberamente. Tuttavia, non è necessaria una costante attività sismica per prediligere soluzioni testate con
movimento e tale preferenza andrebbe accordata anche a
contesti che presentino forti escursioni di temperatura durante
l’anno, o costanti vibrazioni del terreno per la presenza di mezzi
su rotaia sopra e sotto il livello del manto stradale.
Indipendentemente dalla condizione di movimento a cui il
coprigiunto è stato sottoposto in fase di prova, un’altra variabile
importante è il sistema di montaggio del coprigiunto. Le
sigillature possono essere posizionate a diverse “altezze”
all’interno della cavità e non è detto che la configurazione di
prova sia replicabile in cantiere.
La norma richiede di mantenere le condizioni di test e non
variarle. L’unica eccezione è rappresentata dalla configurazione
di prova considerata più gravosa: se il sigillante è stato
certificato dalla parte esposta al fuoco (2); si può applicare
il protettivo anche nei casi in cui lo stesso è più distante dal
fuoco (3) oppure (5).
Il contesto normativo per la certificazione dei prodotti
Tra il 2007 e il 2013 l’omologazione nei Paesi membri dell’Unione di una serie di importanti direttive comunitarie ha esteso a tutta l’Unione Europea criteri comuni per la valutazione delle performance dei prodotti di resistenza al fuoco. Da quel momento i singoli Paesi membri hanno mantenuto al loro interno la definizione delle strategie antincendio, ma è uscita dalle loro competenze e standardizzata a livello Europeo la determinazione dei prodotti che possono essere impiegati per realizzarle, e che a oggi devono essere valutati secondo criteri omogenei e comuni a tutti gli Stati membri. Nel 2007 è avvenuta in particolare l’introduzione obbligatoria delle due classificazioni Europee EN 13501-1 ed EN 13501-2 che hanno definito le classi di reazione e resistenza al fuoco applicabili a tutti i prodotti di costruzione.
Di seguito si riportano tali classificazioni, necessarie per comprendere le performance dei diversi prodotti in ottica comparativa (vedi Tabella 5 e Tabella 6).
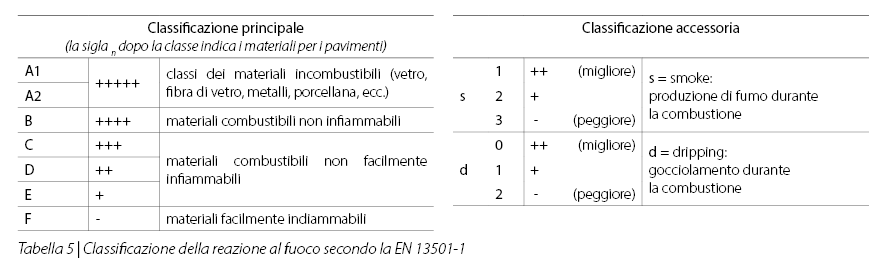
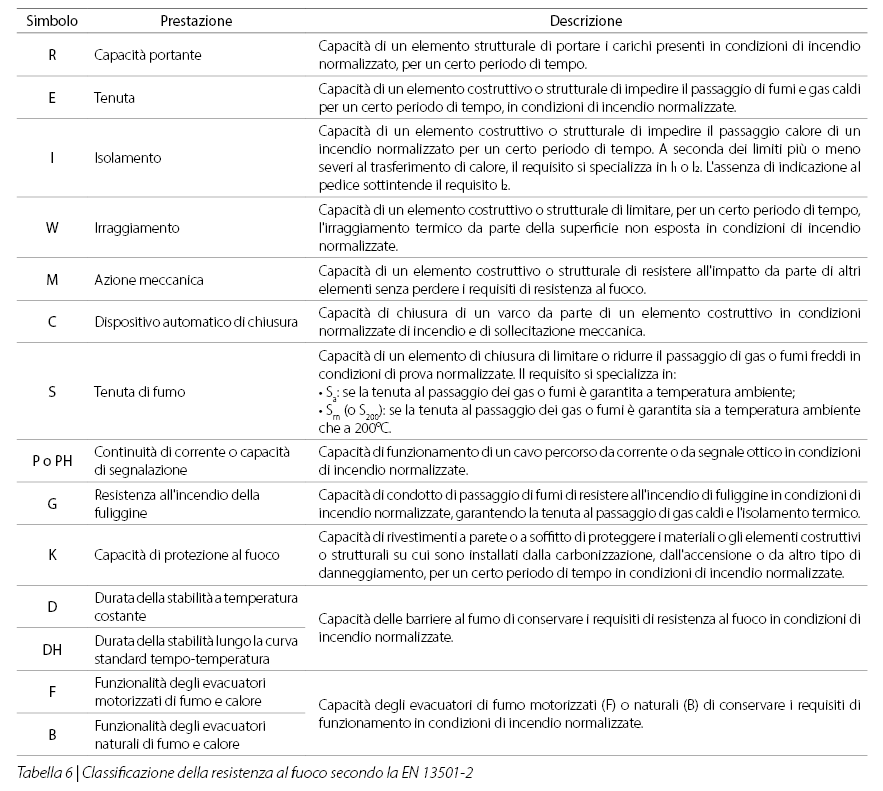
Rapporti di classificazione e rapporti di prova
Le classificazioni Europee di reazione e resistenza al fuoco sono valutabili secondo tre diverse metodologie:
- il metodo sperimentale,
- il metodo analitico;
- il confronto tabellare.
I tre approcci non sono sostituti perfetti: il professionista antincendio ha la facoltà di scegliere il metodo più opportuno tra quelli disponibili, tenendo conto che in alcuni contesti non sono tutti e tre implementabili. Ai fini di questa introduzione approfondiamo il primo dei tre approcci che è spesso il più oneroso e anche l’unico disponibile per la valutazione degli attraversamenti di impianti. La complessità di questo metodo è legata all’esigenza di riprodurre in fase di test tutte le variabili critiche che possono influenzare il comportamento di un sistema protettivo in un caso reale. Per questo, oltre alle temperature di incendio della ISO 834, nei forni di prova viene applicata una sovrappressione, in media di 20 Pa, che tende a spingere verso l’esterno fiamme e fumi rendendo più difficile il superamento della prova. In caso di elementi con funzione strutturale, è inoltre necessario applicare dei pesi che permettano di valutare la stabilità strutturale degli stessi in condizioni di incendio.
Per raggiungere validità Europea le prove devono essere eseguite in un laboratorio accreditato sia dalle autorità ministeriali del Paese che da “Accredia” un organismo sovranazionale che certifica i requisiti minimi di tutti i laboratori ufficiali. La descrizione dettagliata dei risultati di prova e la classificazione di resistenza dei sistemi sono contenuti in due diversi documenti:
a) Rapporto di Prova (documento riservato)
Il documento contiene tutti i dati relativi al campione sottoposto alle prove. Si tratta di un documento di dettaglio, che include oltre alla descrizione verbale dei campioni, disegni e schemi illustrativi dei sistemi di fissaggio utilizzati e delle distanze tra i vari elementi testati;
b) Rapporto di Classificazione (documento pubblico)
Il documento riporta per ogni elemento testato la classificazione ufficiale secondo quanto raggiunto dal sistema in prova. Vediamo alcuni esempi di classificazione tratti da veri rapporti di classificazione che riprendono i concetti visti nei paragrafi precedenti.
La Tabella 7 riporta quattro diversi esempi di classificazione selezionati da diversi rapporti di classificazione reali. Le descrizioni sono tagliate per esigenze di spazio e per gli scopi di questa introduzione, ciascun elemento è spiegato più in dettaglio nel rapporto stesso.
Come si può vedere, ciascun test è associato univocamente a una norma specifica (es. non è possibile testare sistemi di sigillatura di giunti e tubi in un’unica sessione) e a uno specifico orientamento del supporto di prova: “verticale” se il campione è una parete e “orizzontale” se il campione è un solaio. In queste condizioni, ovvero a parità di norma e orientamento, è possibile testare diverse soluzioni, come visibile dal confronto tra la seconda e la terza riga della tabella che mostrano all’interno dello stesso solaio una soluzione con collare e un’altra con applicazioni particolari su pannello: una passerella combustibile e una blindosbarra.
L’entrata in vigore del CPR n° 305 del 2011, ha reso obbligatoria in Europa a partire dal 2013 - con alcune limitate eccezioni - la marcatura CE per tutti i materiali di costruzione per i quali esiste una norma armonizzata di prodotto. All’interno del mondo della protezione passiva, per una vasta gamma di sistemi non esiste una norma di prodotto, ma soltanto una normativa di prova (es. EN 1366-3) per cui non sussiste il requisito di obbligatorietà. Nello schema seguente (Tabella 8) si riporta il quadro aggiornato alla data di pubblicazione di questa guida.
Come si può vedere per porte, tende e serrande esiste una norma di prodotto. Per questo la loro produzione e commercializzazione è obbligatoriamente soggetta a marcatura CE. Il resto dei prodotti di protezione strutturale e sigillatura più comunemente usati non dispone, al contrario, di uno standard di prodotto armonizzato e le prove di resistenza al fuoco organizzate in laboratori ufficiali sono quindi sufficienti a garantirne la validità e la possibilità di applicazione. In realtà anche in assenza di obbligatorietà per ciascuno dei prodotti considerati è possibile richiedere una marcatura CE, passando per uno step intermedio: l’ottenimento di un European Technical Assessment (letteralmente “Valutazione Tecnica Europea” - più comunemente abbreviato con l’acronimo ETA) seguendo i passi previsti dalle linee guida (ETAG o EAD) predisposte per ciascuna tipologia di prodotto*.
L’ETA è un documento che raccoglie i risultati di tutte le prove eseguite su uno stesso sistema presso laboratori accreditati. A titolo esemplificativo, L’ETA di una linea di prodotti denominati “AF Bags” raggruppa in un unico documento tutti gli elementi rilevanti relativi a modalità di posa e performances che si possono trovare all’interno dei diversi rapporti di prova e classificazione in cui tale sistema di sigillatura è presente. I risultati di prova riportati in un’ETA non riguardano esclusivamente le caratteristiche di resistenza al fuoco, ma al contrario possono confluire in questo documento tutta un’altra serie di risultati che il produttore considera utili a qualificare determinate prestazioni del prodotto.
Un elenco di tutte le variabili che possono essere riportate in un ETA per i prodotti di sigillatura antifuoco, estratto dall’EAD 350454-00-1106 (ex ETAG 026 - parte 2) è disponibile nel grafico seguente.
L’inclusione dei risultati relativi a prestazioni diverse da quella principale per cui si certifica un sistema è a discrezione del produttore con l’eccezione di due parametri che sono cogenti: la caratterizzazione chimico-fisica del sistema e la sua durabilità.
La prima di queste due caratterizzazioni permette di garantire l’assenza di sostanze tossiche nella composizione del materiale e di monitorare nel tempo che i prodotti mantengano la stessa composizione, un elemento quest’ultimo imprescindibile per qualificare i prodotti ad essere idonei per la successiva marcatura CE.
La seconda caratterizzazione obbligatoria, ovvero quella di durabilità, permette di verificare per quali condizioni d’uso il prodotto o sistema mantiene inalterato nel tempo il proprio comportamento. A tal fine i prodotti che compongono il sistema di sigillatura sono sottoposti a cicli di invecchiamento accelerato che permettono di simulare in alcune settimane (o mesi) l’impatto arrecato al sistema da determinate condizioni ambientali in un periodo prolungato. Generalmente lo standard di tempo per cui si valida il funzionamento del sistema è di 10 anni, ma è possibile simulare per durate di tempo superiori attraverso un’estensione temporale dei cicli di invecchiamento a cui sottoporre i prodotti.
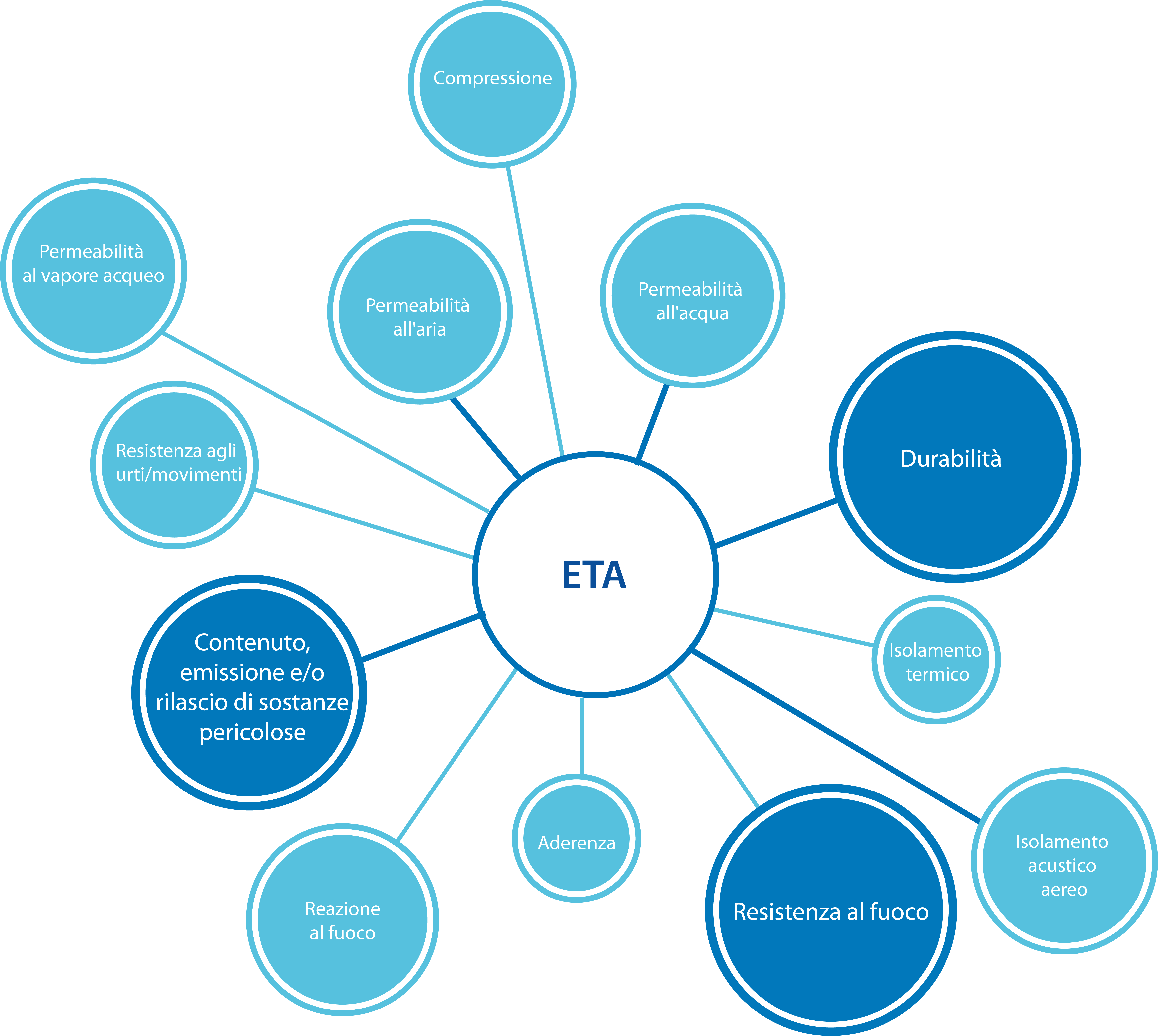
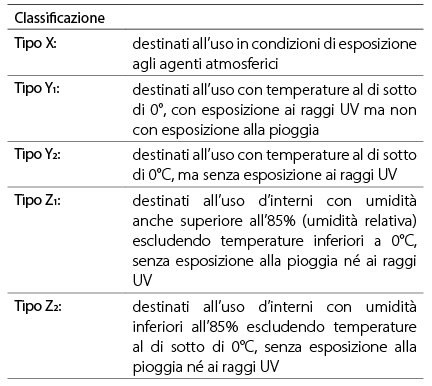
La classificazione di durabilità è importante. Se da una parte l’esposizione diretta ai raggi ultravioletti e alla pioggia sono elementi relativamente trascurabili per i prodotti di compartimentazione, destinati nella quasi totalità dei casi ad ambienti interni e senza esposizione diretta ad agenti atmosferici, d’altra parte è molto frequente l’esposizione ad alta umidità e a temperature che in inverno scendono al di sotto degli 0°C e per questo una caratterizzazione di classe superiore alla “Z” è altamente consigliata. La scelta di AF Systems di utilizzare acciaio inossidabile per la struttura dei propri collari e trattamenti che non risentono dell’umidità o delle escursioni di temperatura va in questa direzione.
Una volta eseguiti tutti i test di resistenza al fuoco, i test cogenti di caratterizzazione chimico-fisica e di durabilità e gli altri eventuali test di prestazione, può iniziare la stesura di un’ETA ad opera di uno dei Technical Assessment Body (Organi di Valutazione Tecnica) nominati dai governi di ciascuno Stato Membro dell’Unione. Oltre a raccogliere tutti i risultati di uno stesso sistema certificato il TAB può richiedere test addizionali al produttore e aggiungere valutazioni tecniche che estendono il campo di applicazione dei singoli certificati. L’ETA emesso in versione temporanea da un TAB deve successivamente circolare per un certo tempo all’interno dell’EOTA, l’associazione che raggruppa tutti i TAB Europei, e che monitora tutto il processo di ottenimento di un’ETA. Se durante questo periodo di circolazione non vengono sollevate obiezioni, o le stesse vengono sanate attraverso addizionali test / presentazione di documentazione accessoria, l’ETA può essere emesso.

Per conseguire questi ambiziosi obiettivi è necessaria l’implementazione di un sistema di controllo di produzione in fabbrica, verificato costantemente attraverso audit eseguiti da professionisti nominati dal TAB di riferimento. Poichè la protezione passiva al fuoco rientra nella categoria di controllo più stringente all’interno del sistema messo in atto dall’Unione Europea, (il tipo 1/1+ del sistema di “Assessment and Verification of Constancy of Performance (AVCP)”) si rende necessaria l’esecuzione di almeno due audit ogni anno per ciascun prodotto soggetto a marcatura CE con la possibilità di ritiro della marcatura eventualmente già rilasciata in caso di gravi non conformità di produzione. Quanto detto permette di capire perchè se l’ETA ha durata indefinita nel tempo, la marcatura CE ha un orizzonte temporale di un anno, e ogni dodici mesi i certificati di costanza di prestazione devono essere rinnovati. Le difficoltà operative appena esposte hanno spinto molte aziende che presentano una separazione tra organizzazione commerciale e produttiva (es. con manifatture esternalizzate o delocalizzate) a porsi come obiettivo finale il raggiungimento di un’ETA e non la marcatura CE.
AF Systems è orgogliosa di essere la prima, e a nostra conoscenza ad oggi ancora l’unica, azienda di matrice Italiana ad avere ottenuto ETA e marcatura CE volontaria per i propri prodotti di sigillatura di attraversamenti di condotte (AF Fireguard 3), tubi e cavi (AF Collar, AF Multicollar, AF Collar C, AF Sleeve, AF Brick e AF Bags) e di protezione antifuoco di giunti di dilatazione (AF Joint e AF Seismic Joint). Il processo di conversione dei rapporti di prova e classificazione in marcatura CE ad ETA e successiva marcatura CE è attualmente in corso anche sugli altri prodotti del nostro catalogo con l’obiettivo di garantire ai nostri clienti di poter sempre contare su soluzioni che raggiungono i massimi livelli non solo di innovazione, ma anche di affidabilità.